Hello everybody,
after the outlets in the SRB chambers except for the two 36’’ feed pipes and the nine missing pipe supports are done, it is now time for the last two outlets behind and under the Tail Service Mast (TSM). 
This initially affects the section behind the rejuvenation of the 24’’ ring line to 16’’ (Ø 2,5 mm) just before the corner of the TSM beside the SSME Blast chamber to 12’’ (Ø 2,0 mm), such as re-measurements have shown. 

Source: nasatech.net
On this pipe sitting eight small bent nozzles, which should have a diameter of about 0,5 mm. 

Source: nasatech.net
In order to adapt this outlet I initially have bent for simplicity a continuous piece of rod Ø 2,0 mm, ranging from the ring line to the end of the nozzle tube under the TSM, which is sitting on two support angles. This way possibly necessary corrections of position and mounting of the nozzles should be made easier, and only when everything matches this nozzle tube is cut at the last rejuvenation and connected to an intermediate piece with Ø 2,5 mm, which begins at the ring line (Ø 4,0 mm). 
Here this continuous pipe is bent, which begins at the ring line.
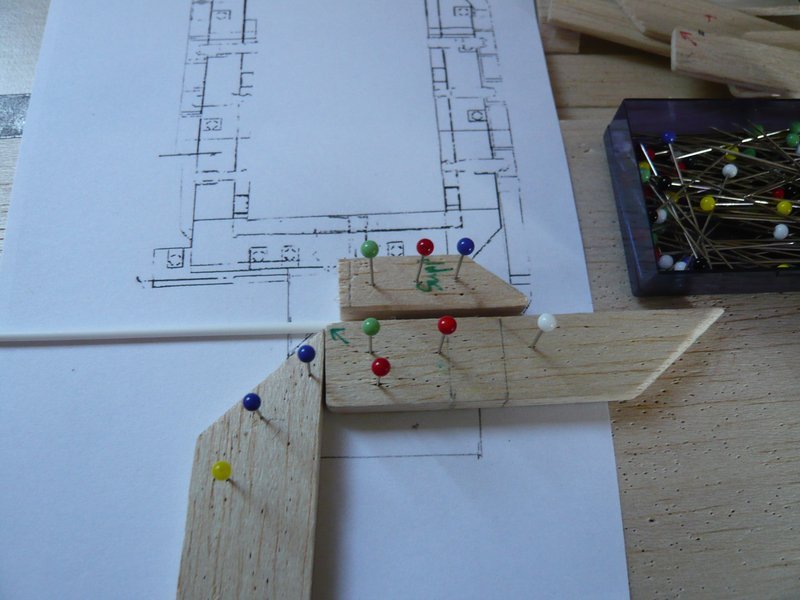
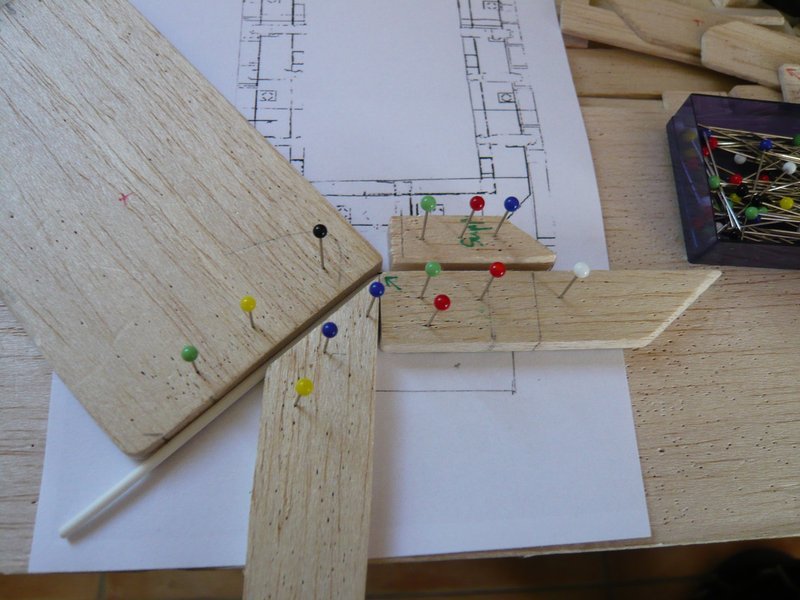

And this is the first test that looks already times quite good, 

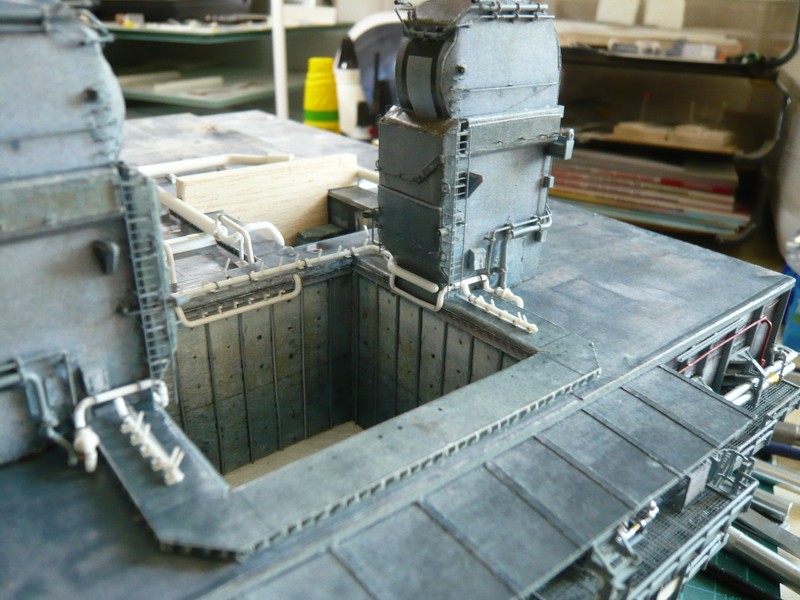
although the tube seems to be a little too close to the TSM corner,

what I’ll be watching in more detail once more. 
meanwhile shape and seat of the nozzle pipe have been slightly modified, and for facilitating the tests I have tinkered a little TSM Balsa dummy to avoid unnecessary stress for the final TSM. 

And hence to the tricky nozzles that had already made some headache a year ago dealing with the nozzle pipe on the rear wall of the SSME chamber. 

Because my former manufacturing method of the individual nozzles in retrospect appeared as being too complicated, I have fiddled about another solution that should be less stressful. 
While on the former almost twice as long tube (approx. 32 mm) were arranged six nozzles, on this tube (about 16 mm) under the TSM this time even eight nozzles with Ø 0,5 mm are to be accommodated, resulting in distances of about 1,4 mm. 
For the marking and drilling I have benefited of a PE template (cmkkits.com) for 0,8 mm rivets, which was very helpful. 
First I have pre-drilled with Ø 0,3 mm and then after that with Ø 0,5 mm.

The idea was to insert somewhat longer rods (about 7 mm, Ø 0,5 mm) into the holes, to glue them with MEK and thereafter to bend all together at one time under moderate hot air in the final form, and then to cut. 

Therefore, the pipe had to be clamped again in a balsa corset, what has proven itself in similar form already several times. 

The required clear height of the nozzle bows results from this close-up on the basis of the reference diameter of the nozzle tube (Ø 2,0 mm) to about Ø 0,6 mm,
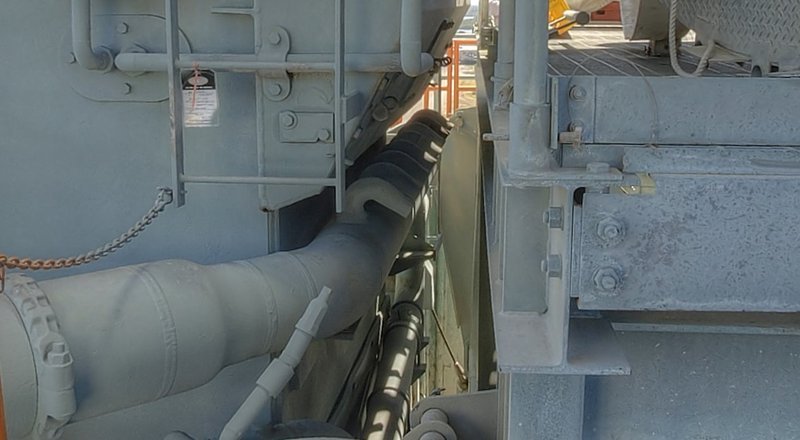
Source: nasatech.net
which is why I now have clamped a corresponding brass rod with Ø 0,6 mm directly behind the nozzle rods, whereby this Balsa jig looks slowly pretty adventurous. 
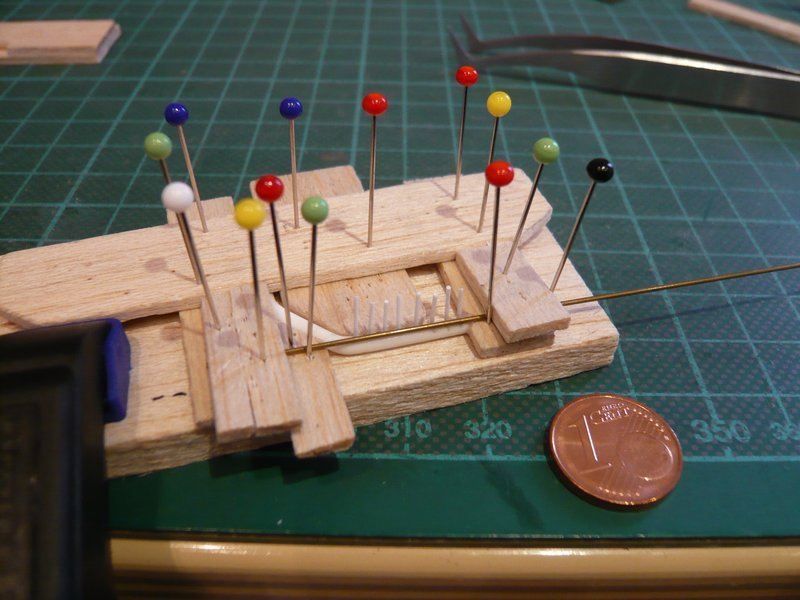
And now the entire row could be bent, the Proxxon Gun in the right hand, and with Left the rods were carefully bent down with a short Balsa slat,
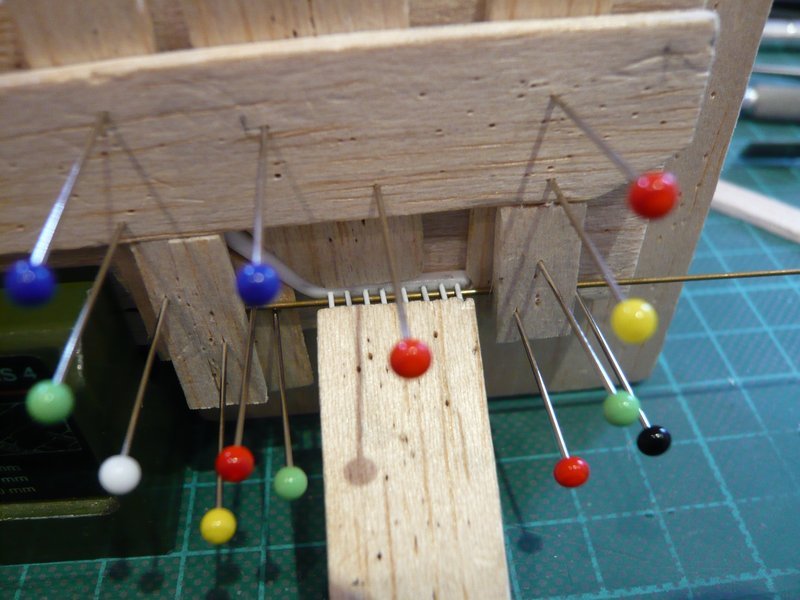
what has worked well straight away. 
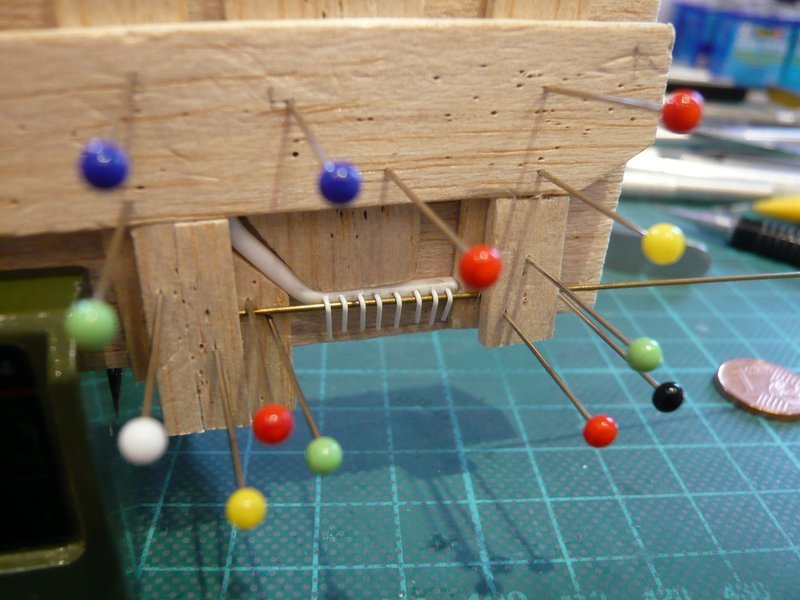
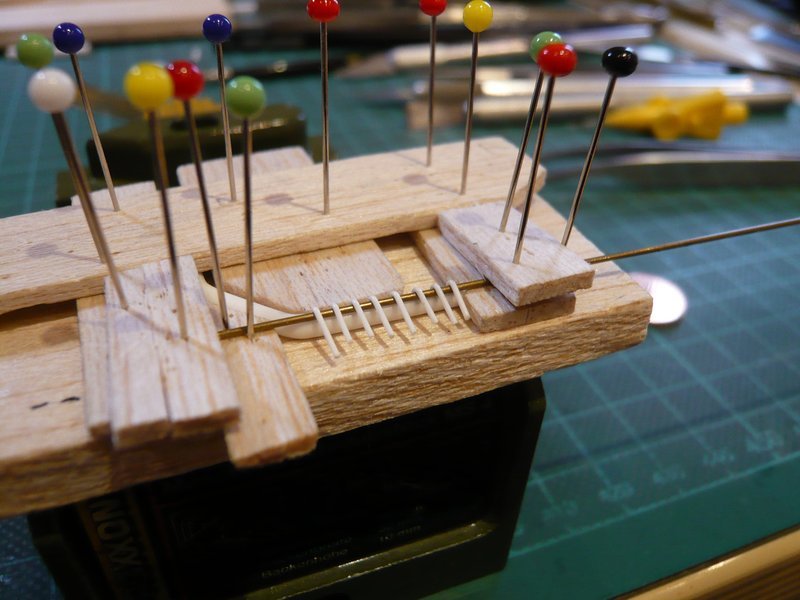
After the nozzle lengths were marked,
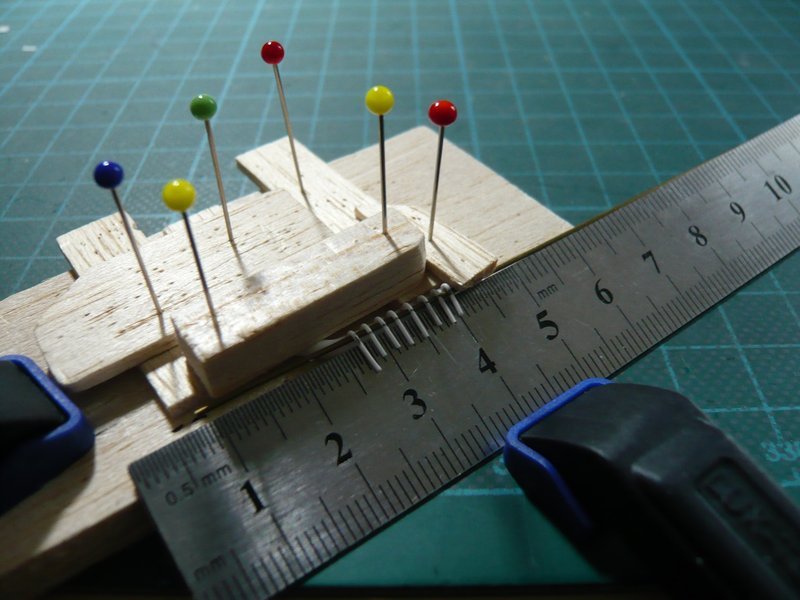
they were cut off on the steel ruler with the cutter chisel.
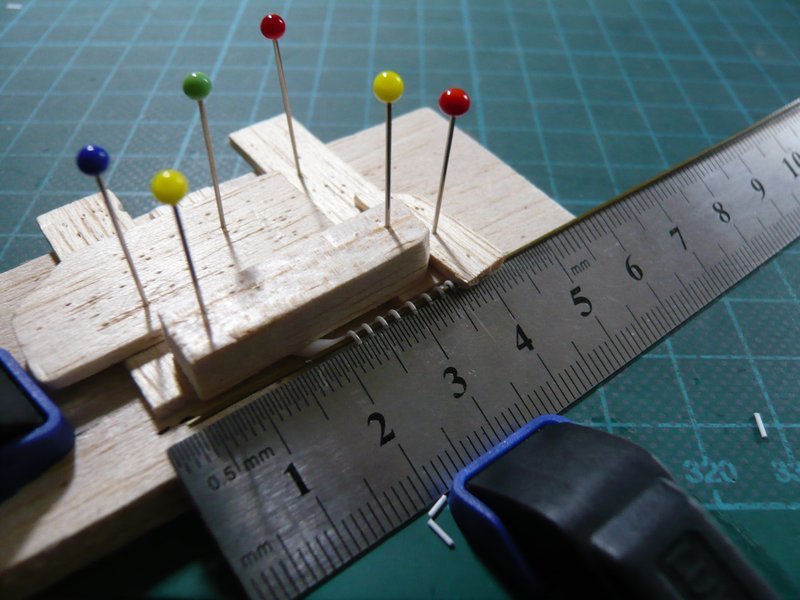
And then it looks like this. 
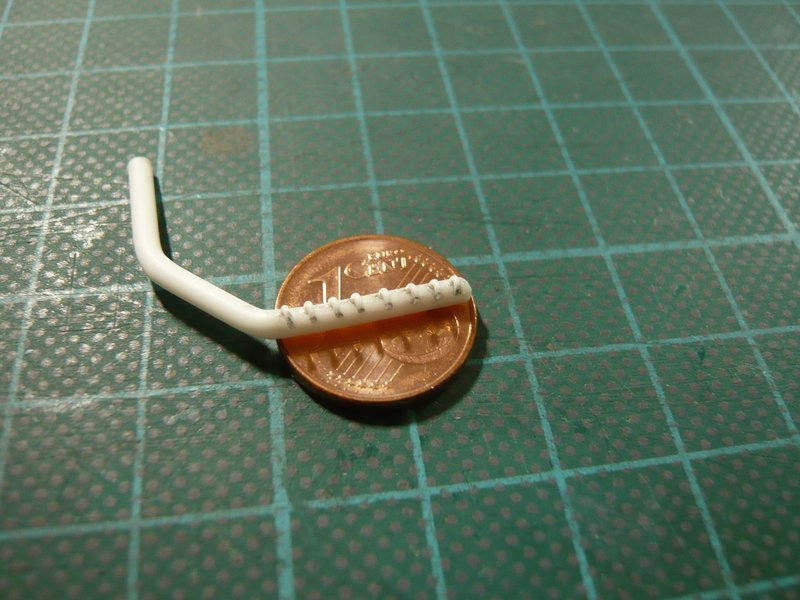
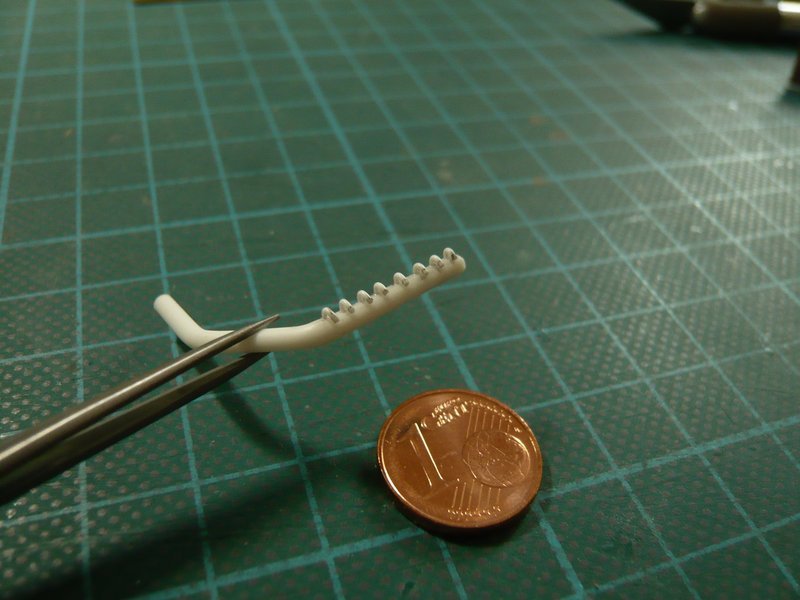
And from this result, I am now totally surprised, because this was not necessarily to be expected. 
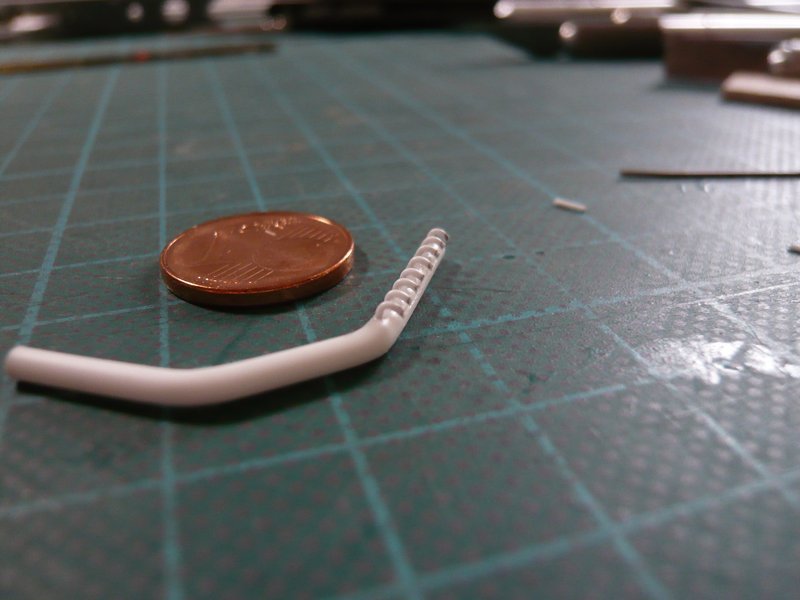
Now I can calmly turn to the nozzle openings, which can tolerate a little bit tuning.
Tomorrow I will test this nozzle pipe on the MLP. 
