Hello friends,
after a long and exhausting search through my previous build report, I found the last post before my Florida trip last October, which was in May 2023 (401/44), which was about the Rainbirds.
…
Source: nasatech.net
Now only a pipe with Ø 6,3 mm must then be fitted with the wide opening and cover, and the shell construction is finished, that could work. 
…
And at this point we can now continue. I hope that it is in the sense of all and that you are still interested in it. 
Hello everybody,
yep, finding the knitting needle was really a stroke of luck, because thus I need only two parts for the tube, because the transition to the conical central part already exists, and can thus save me some work. But just in case I had already set aside some marker pens (Ø 8 mm). 
Then I further thought about to improve the cutting of the bevels for the cover plates. For this I’ve cut a separate 8° cut in my miter-device what sawing makes something easier as with my auxiliary device. That could occur to me even before.
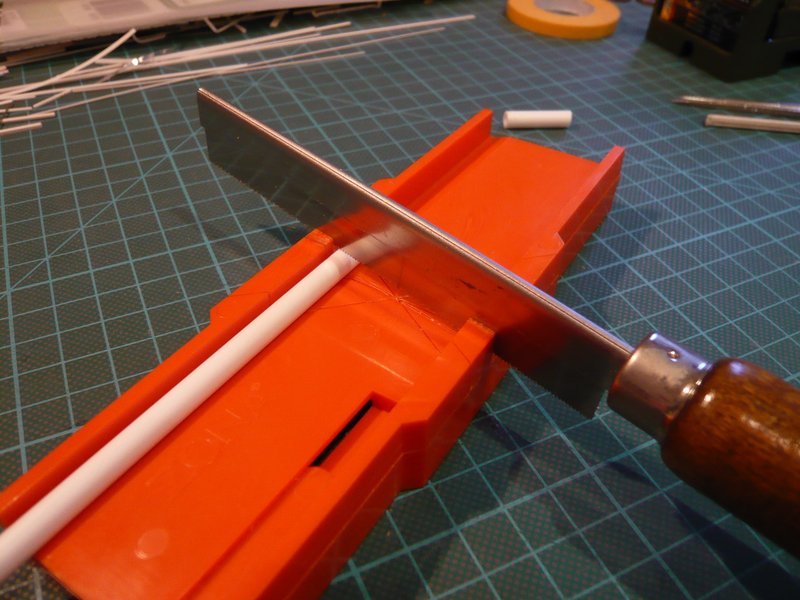
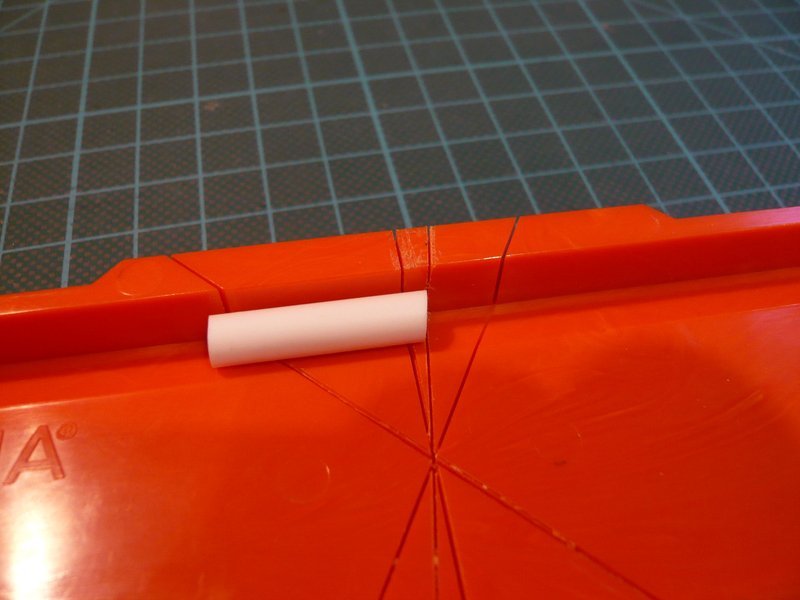
And for marking out and sawing of the openings I have also been thinking a better solution. For that I have marked the opening of a tape and glued to the tube.
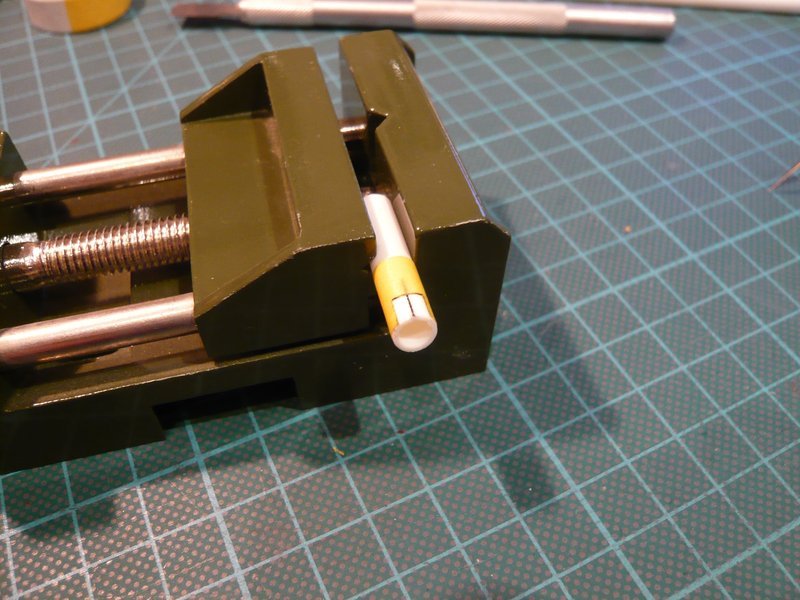
And for the sawing of the opening I have used my Dremel with the small circular saw,
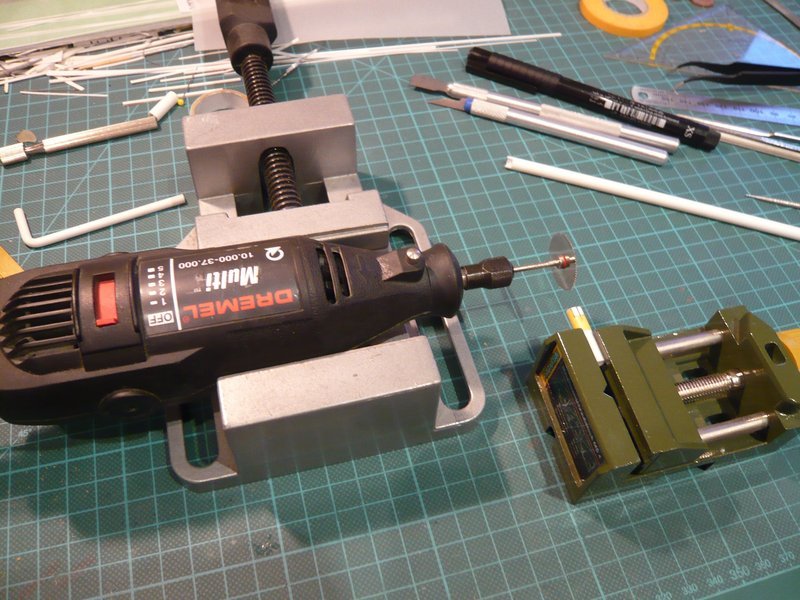
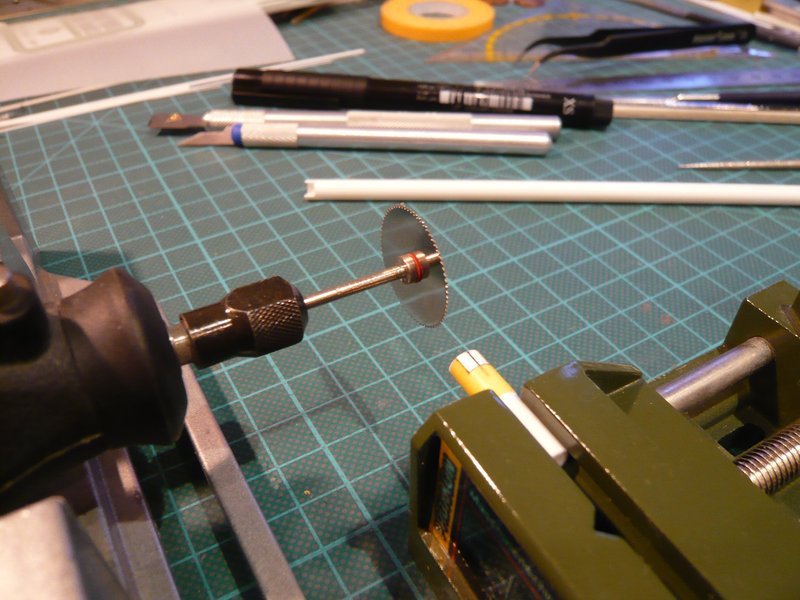
because the openings so should certainly become more accurate, I hope. 
That was a surprise when I’ve realized that I had sawed the opening at the bottom of the beveling instead of at the top,
what nobody has noticed so far.
And that was also the reason for further pretests. 
Here again first with the mini circular saw, but without having sawed the beveling previously.
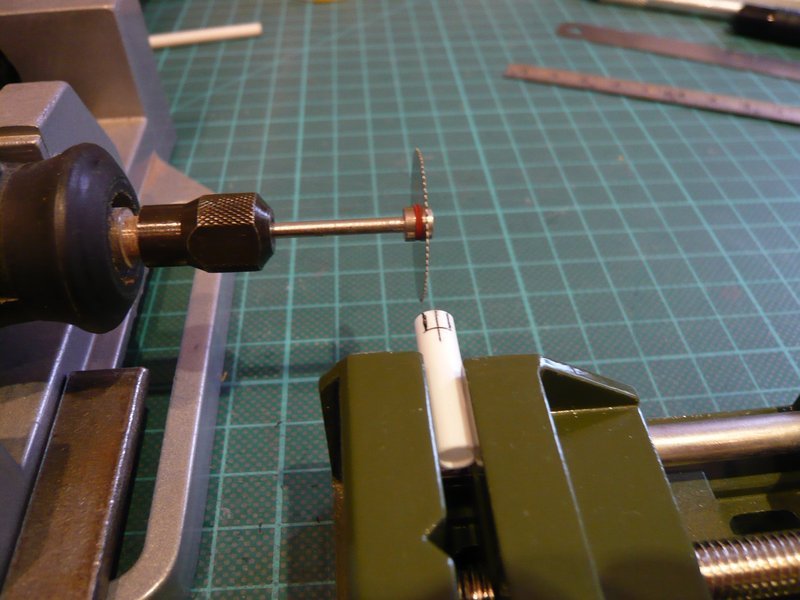
But thereby the markings can also quickly be exceeded, 
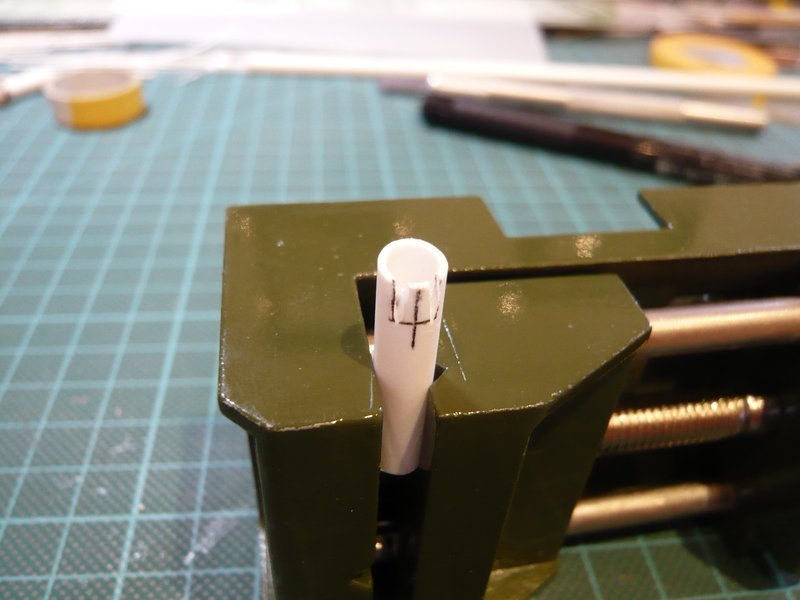
or else be cut as here in another test into the side wall. 
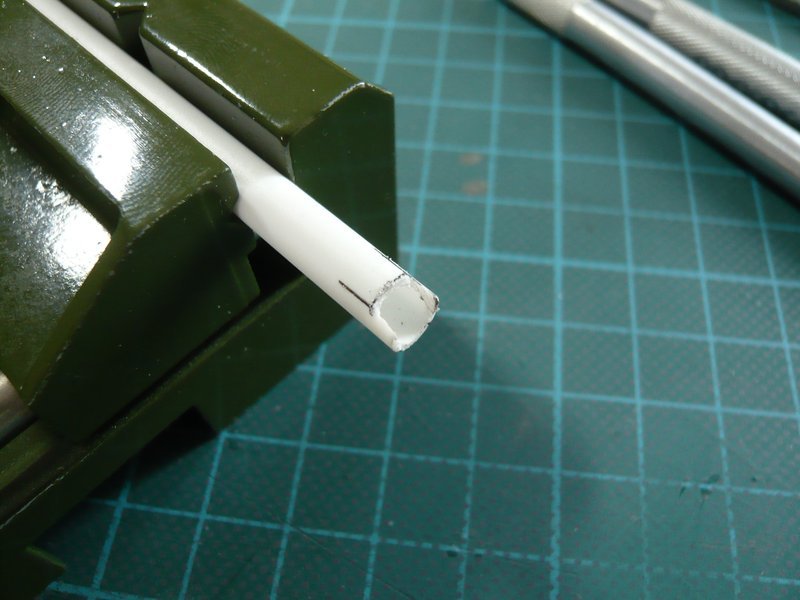
In any case one must still rework the opening,
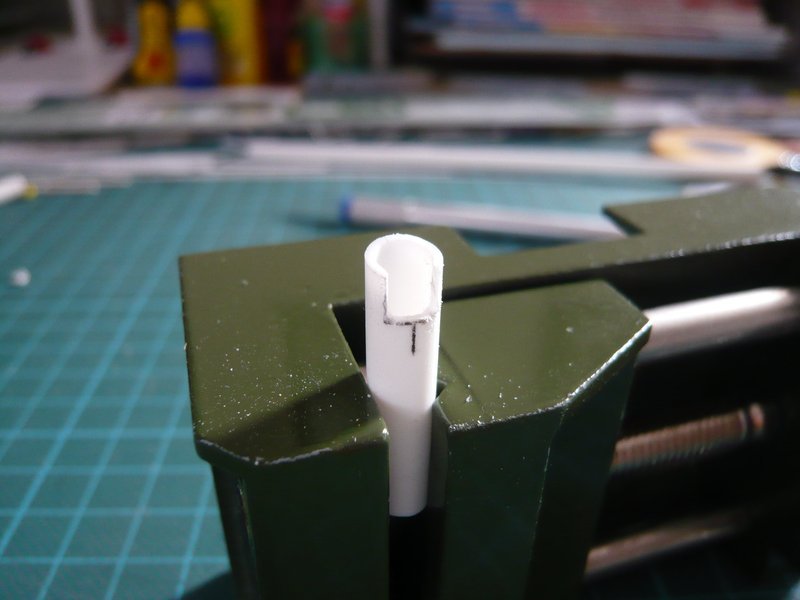
whereby this also can become wider and higher than desirable. 
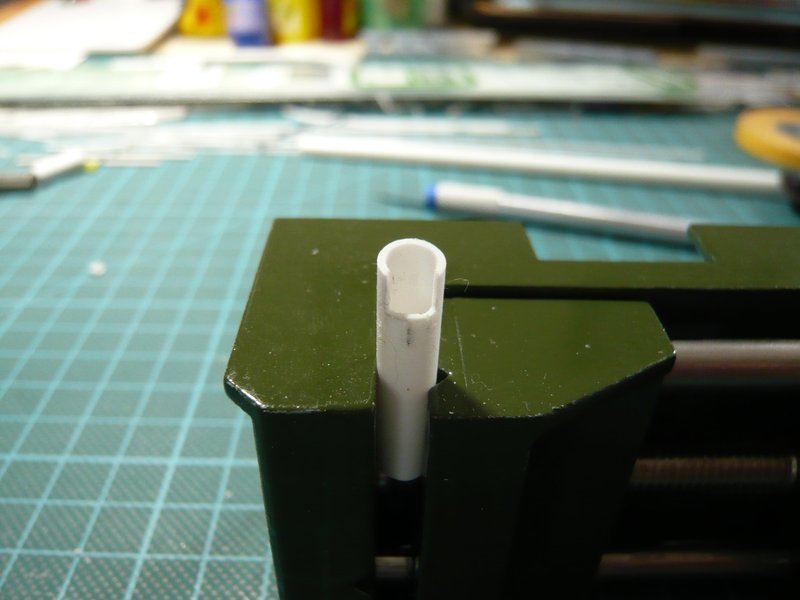
The height can be adapted by making the cut for the beveling a little bit further below. But all in all I’m still not completely satisfied with the results of the saw method, especially as I have also noticed that probably the spindle or the clamping sleeve of my Dremel has a slight blow which is transmitted to the saw blade. 
That’s why I tried yet another method, where far fewer swarfs arise, and therefore seems to me much more sympathetic. 
For that I have used this cutter blade with straight blade, which can be applied as a wood chisel.
For that I have pushed the tube to a suitable drill shank and then carefully gouged out the opening, what has worked very well.
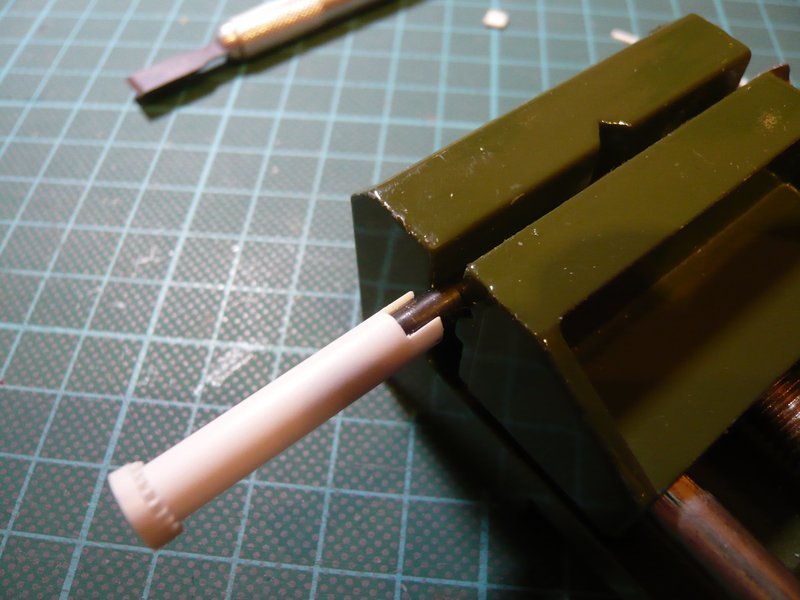
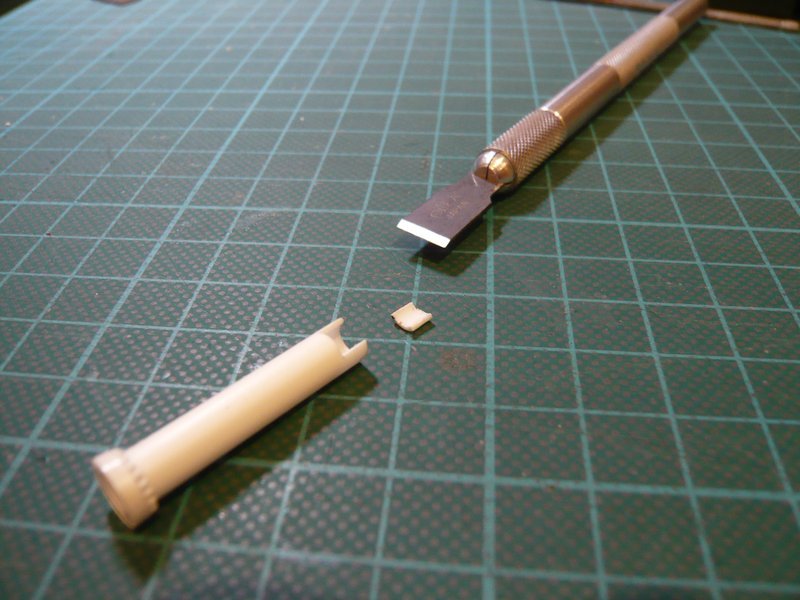
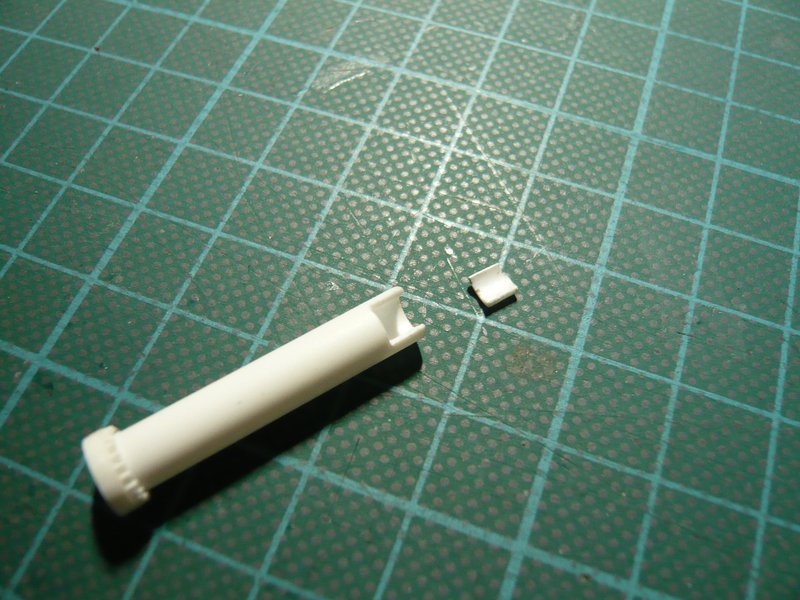
And as one can see, the edges are immediately much more accurate and cleaner than with the saw method and require almost no post-processing.
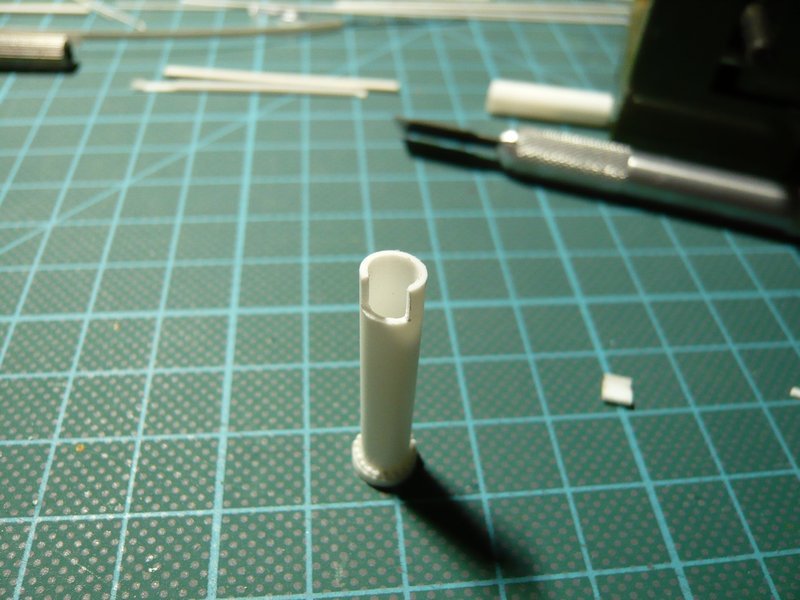
And the beveling can also be subsequently attached smoothly.

And that’s why I will now apply this simpler and more accurate method. 
