Hello everybody,
well, the garden asks incidentally so its toll on those hot days.
But I still tried to keep going and finally the small series of Pipe Supports Type 2 to start, which I so need only 5 pieces. 
First to the preparation of the required items, as there would be the base plates (3 x 3 mm), feet (Ø 1,7 x 0,5 mm), the cover plates (2,5 x 3,5 x 0,25 mm) for the small sickles on which the pipes lie, and even sickles (0,25 mm). For this I’ve used my Punch&Die-Tool with 4 mm diameter as used already for the prototype.
In order to obtain possible a uniform height of 1 mm at the lowest point of the curve, I have used a corresponding spacers in the tool. And then it went on with punching, where you have to watch that one holds the punch vertically, since a small amount of play is present and the base plate is made of aluminum, which is not the last word. 

After that, I marked out in the strip 3 mm width of the sickles, which was quite a torture for the eyes,
because this possible should be centered.

Then I have individually cut the sickles, but this is not quite succeeded, especially since there were a certain scattering of widths.
Aside are the discs (Ø 1,7 mm) for the short legs and the base and upper plates.
To make things worse, I have the sickles but not stored in pairs, so it was all messed up, what you can see here! 

Although I have tried to sort the couples still halfway through laborious remeasuring, these couples were still relatively unequal, which would have meant complicated reworking. That’s why I’ve punched again a 2nd row and made it somewhat more accurately,

where I have tried starting from the middle to uniformly cut the couples on the ruler to 3 mm in length, as it were “hand-picked”. 

And thus the construction of the following supports was also more reproducible,


and thus also more evenly.

And so it went on, three type-2 support still missing,

which followed immediately, so these six supports for the SRB Blast Shields finally are now complete. 

Now let’s go on with the small series of Type 1 Supports, which are arranged around the two SRB holes and carry the thick 24’’ SSWS line. Of which I need, after all, still 29 pieces, for what first had to be prepared a whole lot of small parts. 
First, I have made the small sickles and this time I have acted differently. For that I have laid the sickle strip under a steel ruler, so that they overlap in each case 1,5 mm outwards, and then I have cut the sickle in each case 1,5 mm from the center behind the ruler edge that served as a stop for the cutter. And that worked really better and yielded 3 mm long sickles that have been straightened out a little here and there, if necessary. 


Then I’ve cut the 3 x 3 mm base plates and marked the centers for the holes, and then even punched the missing disks for the feet. 
Now missing only the cover plates from Evergreen channels, which I’ve also cut by measuring with the steel ruler with 3,5 mm length, whereupon a safe stop has proven to be very helpful. 

And so now everything is ready for the mounting of the supports, which will be the grand finale. 

Yeah, that was a hard test of patience and pure stress for my old eyes, because I needed the head magnifying glass,
and sneezing was strictly forbidden! 
BTW, these parts are really tiny, and a few times I had to dive back down to the floor to look for the breakaways. 
Only good thing I got myself some extra sharp tweezers,
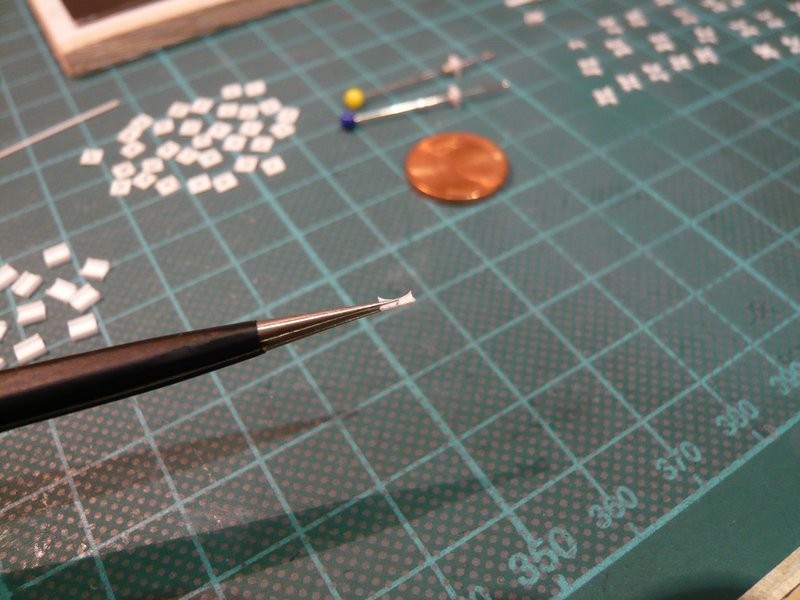
otherwise you get these things hardly to grasp. 
Let’s see how long that will take until all supports are finished, because those are a lot of hand grips, but there I have to struggle through, for better or worse … 
And later all the tiny crazy clamping rings are waiting for me … 
