Tim, credit is due! While I executed the idea well, there would be no idea with the spark you provided. That kind of kickstart has happened many times in my career. Here’s a good example. In the early 90s, Engelhard, where I worked had been trying to shrink itself to success (spoiler alert: it didn’t work). As the head of training, with nothing but layoffs for three years, we had a heck of a time to generate full classes and weren’t doing any training at all. The fellow who ran HR IT, made a casual remark at a staff meeting, “There are lots of other comnpies around here, perhaps you could pool your resources?” That was it… one line. I said it was a brilliant idea. It took nine months to create the Metro Park Consortium, where 6 corporations joined forces to provide for general management education. Turning an idea into an innovation involves a lot of perspiration. I was the CEO of this effort and it worked great. We only needed one or two of our people needing the training and they could get it at the same price as it would cost us internally. Unfortunately, I too was laid off that September in 1995, but the company asked if I would stay to run the consortium. Unfortunately for them, but fortunately for me, I was already hired at Henkel with a better job and a company that’s still paying my retirement 20 years after I left them.
Worked on the second set of annular rings today, with a break to go to the hobby shop to pick up more 0.040" large sheet styrene. When he special ordered the large sheets for me months ago, he ordered more than I needed. He still had it and I bought more.
I measured the rings for the projectile flat, cut it all out and found that my i.d. was about 1/32" too big and wouldn’t work. That’s part of the reason why I was running out of my original stock. I remeasured and re-scribed. For the first of the two rings, I scribed the circumferences and then made radial scribes to faciliate snapping off the scrap.
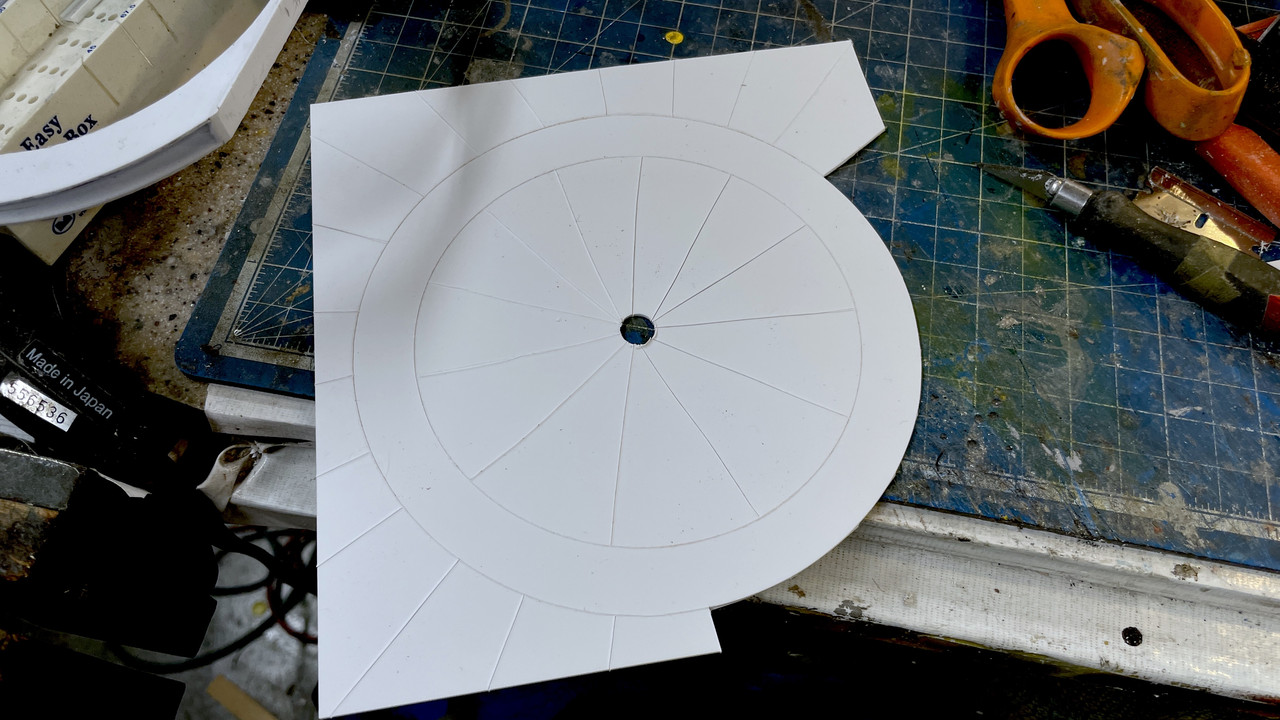
While this works okay, it’s a bit tedious and also leaves some inconsistencies that need to be sanded out. On the second ring, I realized that if I scribed the circles just a bit deeper, I coud snap the scrap out directly, leaving a much smoother and rounder edge. It also took 1/3 the time.
I also was being really anal and actually laid out the 1/6 spacing for the internal bracing. An absolutely meaningless exercise that will never, ever be seen by anyone. But it was fun.
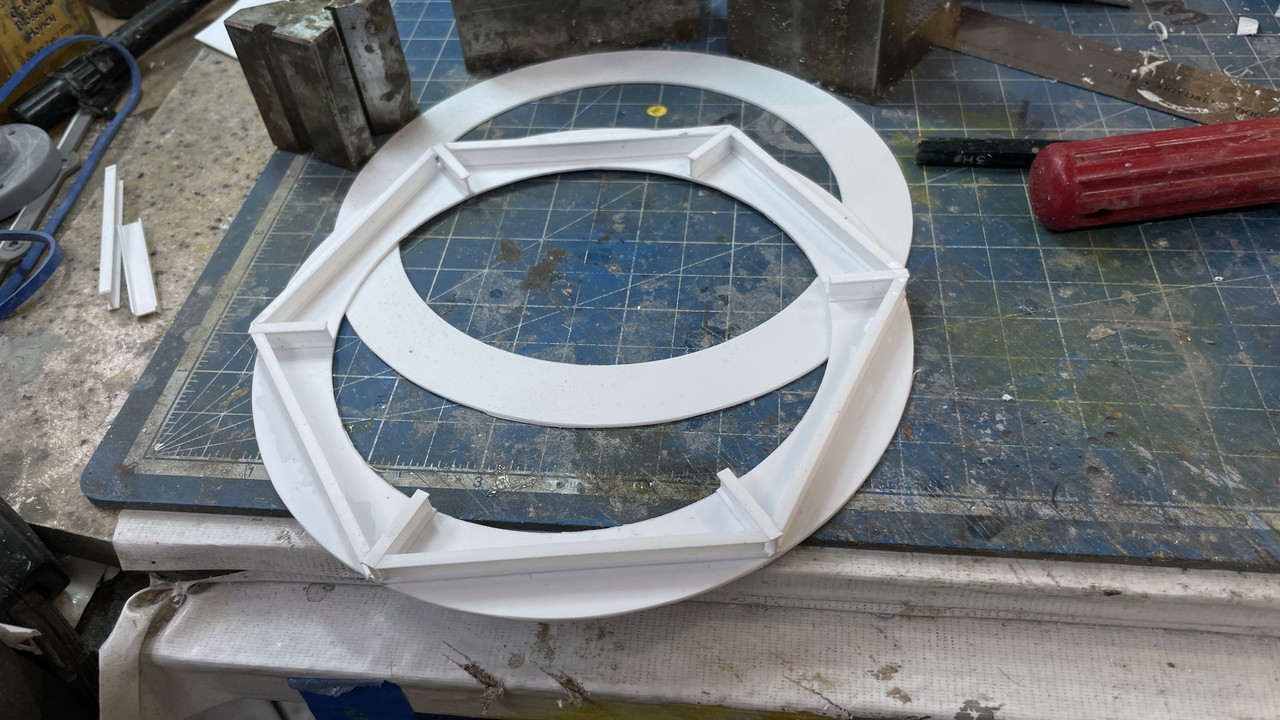
To glue on the top piece I used some angle blocks to hold the edge in line. Liquid cement all the way.
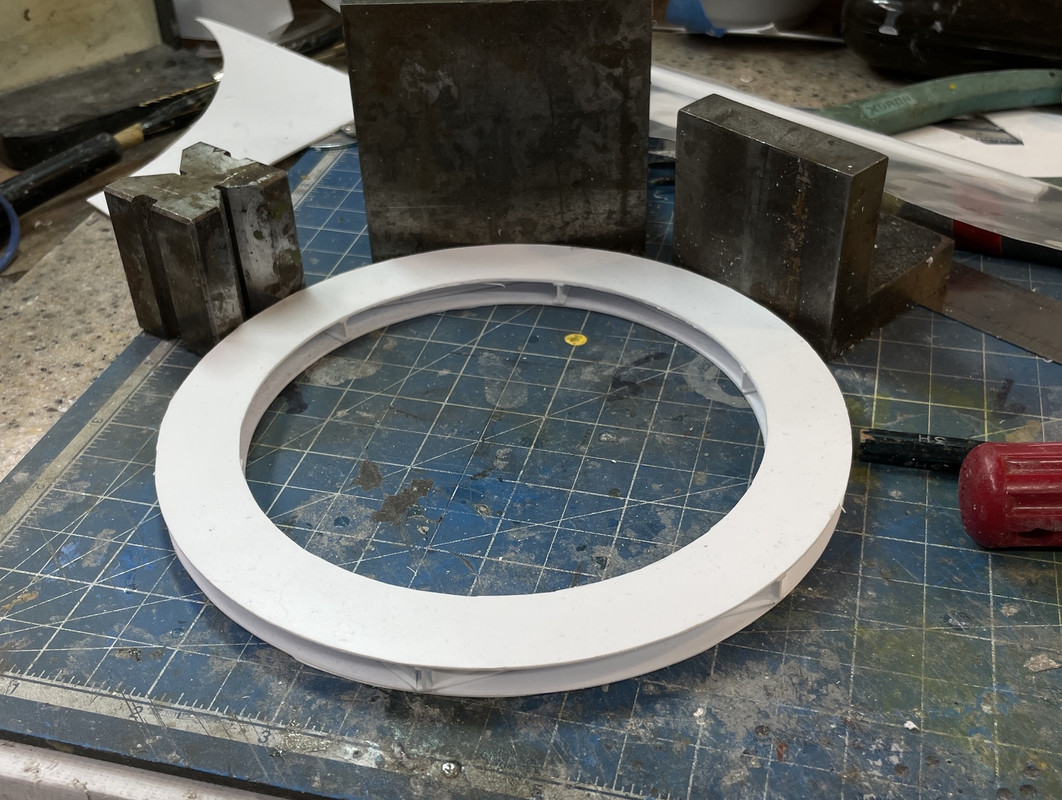
I test fit the stack to see how it all aligned.
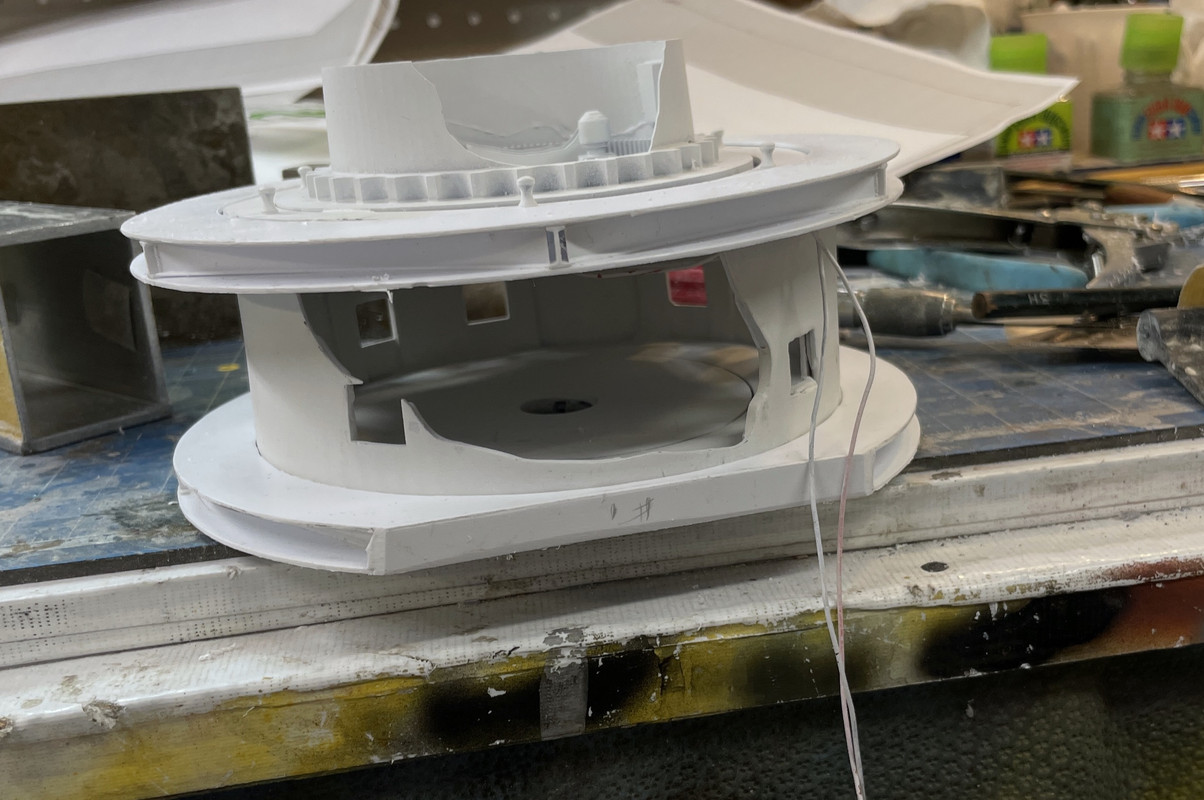
And then I fit the upper and lower annular rings into the drum and was rewarded with a nice rounded drum. I was almost tempted to glue it at this point, but it was very near quitting time and I didn’t want to do anything rash. I’ve said it before, “I am not patient! I am persistent!” It’s that persistence that has me doing stuff two or three times until I perfect the method, but I will screw up when I don’t allow time for glue or paint to dry.
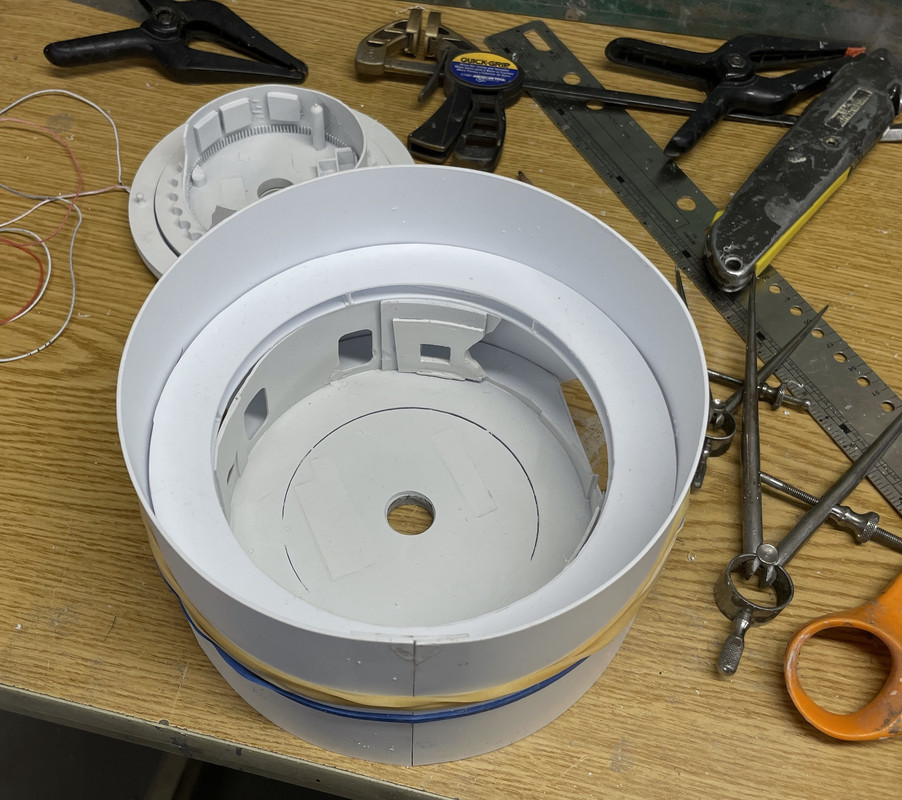
I’ve created the development drawings of the barbette pieces. I don’t have a working CorelDraw any longer, and am not in a position at the moment to buy a piece of $400 software. I have Inkscape and MyDraw. Both are decent, but neither works for me to make full size templates on US Standard Letter Pages.
Coreldraw is simply the best vector drawing program I’ve tried. It does several things that really help. First, it enables you to move the ruler origin anywhere on the drawing page. It makes it so much easier to establish accurate guidelines when you can set zero at the edge of the object. It also enables you to tile prints that exceed the size of your printer’s page. I can’t figure how to do this in MyDraw at all, and in Inkscape you have to export pieces of the drawing as separate PDF files, which is a total pain in the butt!
I ended up printing a page scale image of the three templates with their 1:1 dimensions. Two of them are fully rectangular and will be easy to layout on the styrene. The other has a simple curve on top and bottom edges and I will work that out somehow. Corel also enables scaling very easily. I also have skill with Adobe Illustrator and found it too to be clunky and difficult to use.